Real Time Welding Monitoring System Market By Application
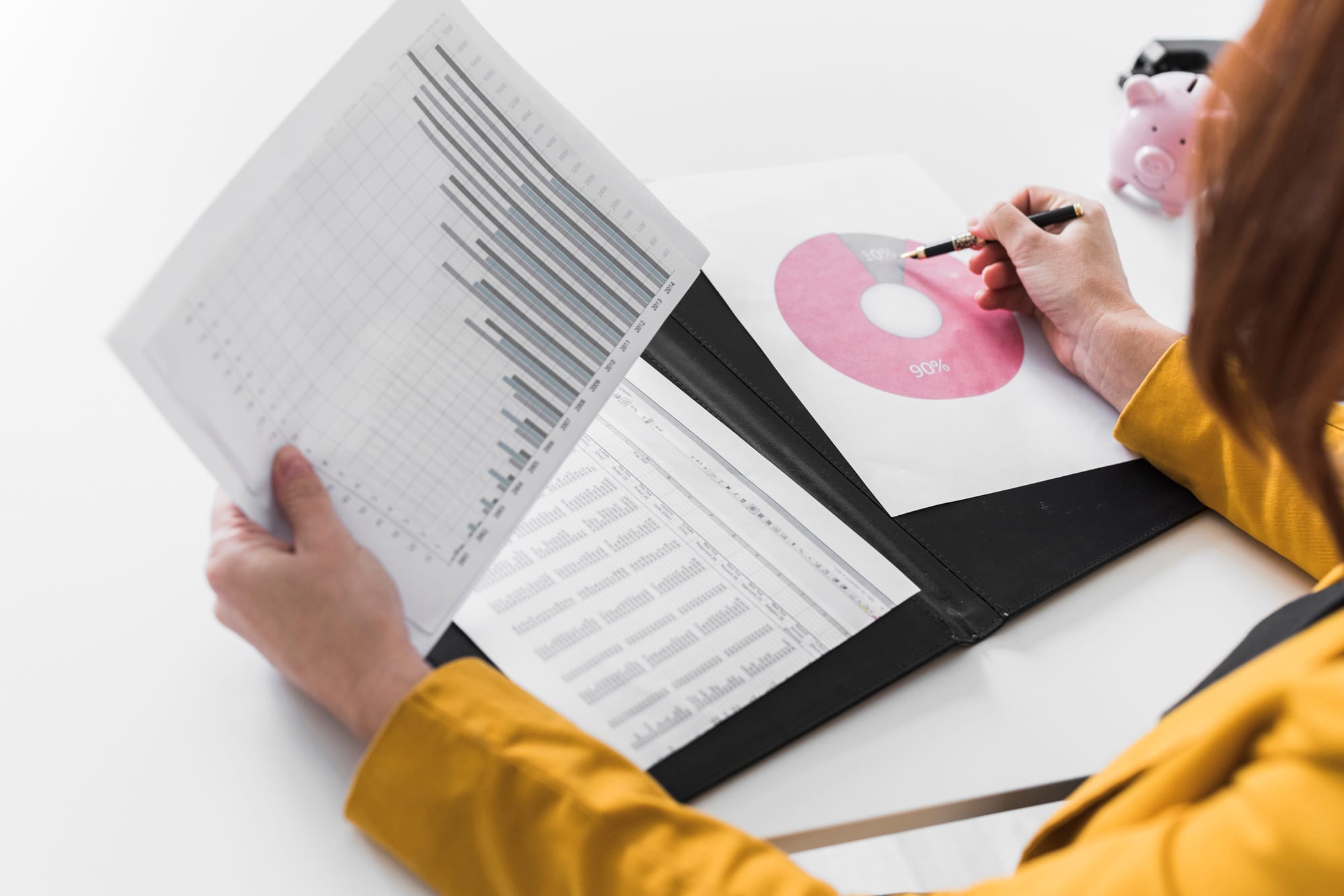
Real Time Welding Monitoring System Market By Application
The Real Time Welding Monitoring System Market By Application size was valued at USD 1.32 Billion in 2022 and is projected to reach USD 2.62 Billion by 2030, growing at a CAGR of 9.3% from 2024 to 2030. The increasing adoption of automation and Industry 4.0 in the manufacturing sector has led to significant growth in the demand for advanced welding monitoring solutions. These systems provide real-time data on the welding process, enhancing efficiency and ensuring high-quality welds. Furthermore, the rising need for safety and quality compliance in industries such as automotive, aerospace, and construction is driving the Market By Application growth.
Technological advancements in sensors, cloud computing, and AI integration are expected to further boost the Market By Application. As industries continue to focus on precision and cost reduction, the need for real-time monitoring systems that can analyze welding data and optimize operations is becoming critical. With increasing investments in smart factories and welding technologies, the Market By Application is expected to witness rapid growth throughout the forecast period. The Market By Application's expansion is also supported by the growing awareness of the benefits of predictive maintenance and reduced downtime in industrial operations.
Download Full PDF Sample Copy of Market By Application Report @
Real Time Welding Monitoring System Market By Application Research Sample Report
Real-Time Welding Monitoring System Market By Application by Application
The real-time welding monitoring system Market By Application has seen significant growth in recent years, owing to advancements in automation and the growing need for precision and quality control in welding processes. This Market By Application includes several important applications that span various industries such as mechanical engineering, automotive, aerospace, oil and gas, chemical, medical technology, and electrical industries. Each of these sectors benefits from the integration of real-time monitoring systems, which not only enhance welding quality but also improve operational efficiency, reduce costs, and ensure regulatory compliance. This report delves into the applications of real-time welding monitoring systems within these industries, exploring the specific needs and benefits that they bring to each sector. Additionally, it identifies key trends and opportunities within the Market By Application that are expected to drive growth in the coming years.
Mechanical Engineering
In the mechanical engineering sector, real-time welding monitoring systems are crucial for ensuring the quality and consistency of welds across a variety of applications, such as machinery manufacturing, structural components, and heavy equipment. The demand for precision and repeatability in mechanical components has driven the need for advanced monitoring tools that provide data on temperature, pressure, and other variables during the welding process. These systems help identify issues such as weld defects, inconsistencies, or process deviations early, preventing costly errors and enhancing the overall reliability and performance of mechanical systems. This results in more durable and efficient mechanical products while minimizing downtime and reducing waste.
Moreover, the use of real-time welding monitoring in mechanical engineering supports the growing trend of automation and digitalization within manufacturing processes. As industries continue to adopt Industry 4.0 technologies, the integration of monitoring systems with automated welding machines ensures that welds are performed with greater accuracy and less human intervention. This trend not only improves the speed of production but also enhances safety and reduces human error, contributing to a more efficient and cost-effective manufacturing environment. As the demand for complex and high-performance mechanical parts increases, real-time monitoring systems are expected to play a pivotal role in meeting these challenges.
Automotive Industry
The automotive industry is one of the most significant adopters of real-time welding monitoring systems due to the precision and consistency required in the production of vehicle parts. From body assembly to the fabrication of internal components, welding plays a critical role in the manufacturing process. Real-time welding monitoring systems are used extensively to ensure that welds meet the necessary structural and safety standards, providing manufacturers with immediate feedback on the quality of each weld. This level of monitoring allows manufacturers to detect issues such as insufficient penetration, distortion, or heat-affected zones, thus improving the overall strength and durability of vehicle structures.
As the automotive industry continues to move toward electric vehicles (EVs) and lightweight materials such as aluminum and high-strength steel, the need for precise and efficient welding processes has intensified. Real-time monitoring systems help automotive manufacturers adapt to these new materials, providing real-time insights into the weld quality and ensuring that the unique characteristics of these materials are properly addressed during production. Furthermore, the integration of monitoring systems with robotic and automated welding systems enhances production efficiency and reduces human error, which is critical in maintaining high production volumes while meeting stringent quality standards.
Aerospace
The aerospace industry requires the highest standards of precision and quality in manufacturing, especially when it comes to welding processes used in the construction of aircraft and spacecraft components. Real-time welding monitoring systems are integral in this sector, ensuring that the welds made on critical components, such as fuselage sections, engine parts, and wing structures, meet stringent safety and performance standards. These monitoring systems provide detailed data on parameters such as heat input, weld bead shape, and cooling rates, allowing for real-time corrections during the welding process and preventing defects that could compromise the integrity of the aerospace components.
With increasing demands for lighter, stronger, and more fuel-efficient aircraft, aerospace manufacturers are turning to advanced materials such as titanium alloys, carbon fiber composites, and other high-strength materials that require highly controlled welding processes. Real-time monitoring systems help ensure that welds on these materials are precise and that any issues, such as thermal stresses or metallurgical inconsistencies, are detected and addressed immediately. This capability not only improves the safety and reliability of aerospace products but also reduces the need for costly rework or testing later in the production process, which can be both time-consuming and expensive.
Oil and Gas
The oil and gas industry presents unique challenges for welding, particularly in the construction and maintenance of pipelines, offshore platforms, and refineries. Real-time welding monitoring systems are critical for ensuring the integrity and safety of welds in this harsh and demanding environment. The monitoring systems help detect potential issues such as joint misalignment, insufficient weld penetration, or inconsistent heat input, which can lead to leaks or failures in critical infrastructure. By providing real-time data, these systems enable welding operators to adjust parameters on-the-fly, ensuring that each weld meets the necessary strength and durability requirements for the specific operating conditions of the oil and gas environment.
As the oil and gas industry continues to explore deeper offshore drilling sites and expand operations in challenging environments, the use of advanced real-time welding monitoring systems becomes even more essential. These systems enhance the ability to conduct high-quality, consistent welds on large-scale projects, often under extreme conditions such as high-pressure or corrosive environments. Furthermore, real-time monitoring provides an effective solution for improving weld quality in remote locations where skilled labor may be limited. The integration of these systems can also result in long-term cost savings by reducing the frequency of weld-related failures and the need for costly repairs or replacements in critical infrastructure.
Chemical Industry
In the chemical industry, welding is used extensively in the fabrication of pipelines, storage tanks, reactors, and pressure vessels, all of which must meet rigorous safety standards due to the potential risks of hazardous materials. Real-time welding monitoring systems are essential for ensuring that welds in these critical components meet the required mechanical properties and integrity standards. By continuously monitoring key parameters such as heat input, voltage, and arc stability, these systems help identify defects such as porosity, cracks, or undercuts, which could jeopardize the safety of chemical plants and refineries.
In addition to improving safety and quality, real-time welding monitoring systems offer significant advantages in terms of operational efficiency and compliance with regulatory standards. By providing immediate feedback on the quality of each weld, manufacturers can minimize the need for rework, reducing downtime and material waste. Moreover, the data collected from these systems can be used to generate detailed reports for quality control and certification purposes, ensuring that the final products meet all necessary regulatory requirements and are safe for use in chemical processing environments. With increasing demand for more sustainable and energy-efficient processes, the chemical industry’s reliance on these advanced monitoring systems is expected to grow.
Medical Technology
The medical technology industry relies on welding for the production of various critical components, including surgical instruments, implants, and medical devices. In this sector, precision and cleanliness are of utmost importance, as even minor defects in welds can compromise the functionality or safety of medical products. Real-time welding monitoring systems help ensure that welds are performed according to the highest standards, providing real-time data on key parameters such as weld consistency, temperature, and pressure. This capability is particularly important in the production of implants and devices that require
For More Iformation or Query, Visit @ Real Time Welding Monitoring System Market By Application Size And Forecast 2025-2030